一、传统工业设计是否已经触及天花板?
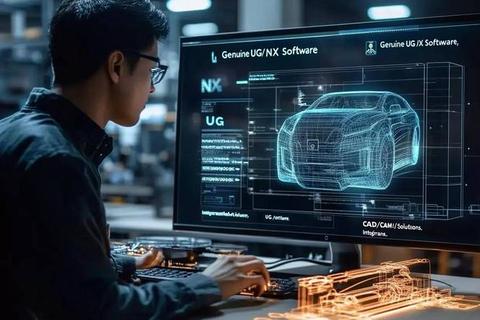
在汽车制造领域,某德系车企曾耗时18个月完成新款发动机设计,却在样机测试阶段发现冷却系统存在结构性缺陷,直接导致2.3亿元研发资金浪费。这样的故事并非孤例——全球78%的制造企业仍在依赖经验驱动的试错模式,设计变更引发的成本占据总开发费用的40%以上。当数字化浪潮席卷制造业,
NX软件颠覆性革新 智造未来设计新视界巅峰领航正在改写这一困局。
二、AI如何打破设计效率瓶颈?
在航天设备制造商洛克达因的案例中,NX的生成式设计模块仅用72小时就完成了传统需要6周时间的推进器支架设计迭代。通过机器学习算法对20万组历史设计数据建模,软件自动生成的蜂窝状拓扑结构成功减重37%,同时提升载荷强度15%。这种
AI驱动的参数化设计并非简单替代人工,而是构建了"设计师提需求-系统出方案-专家做决策"的新型协作模式:
语音指令识别准确率提升至98%,工程师可用自然语言调用2000+复杂命令
几何特征自动识别系统将标准件选型效率提高4倍
基于Simcenter HEEDS的多目标优化,可在72小时内评估1200种设计方案
三、拓扑优化如何重构轻量化极限?
医疗设备厂商美敦力在人工关节开发中,借助NX Topology Optimizer实现了革命性突破:
1. 将CT扫描数据直接转化为参数化模型,自动生成仿生骨小梁结构
2. 通过应力分布云图智能调整材料分布,关键部位强度提升42%
3. 集成增材制造模块,将传统需要17道工序的制造流程压缩至3步
这种
从功能需求反推设计形态的逆向工程思维,正在重塑汽车底盘、航空发动机叶片等复杂部件的开发范式。数据显示,采用该技术的企业平均减少物理样机制作次数5.8次,开发周期缩短31%。
四、数字孪生如何打通制造全链路?
特斯拉上海超级工厂的实践印证了NX数字孪生技术的价值:
冲压车间虚拟调试系统将设备调试时间从45天压缩至9天
焊装生产线通过实时仿真提前发现156处干涉风险
总装环节的AR辅助系统使新员工培训效率提升300%
更值得关注的是
跨学科知识库的构建——NX将材料科学、流体力学等12个学科的超400万条工程知识封装为可调用模块,工程师设计注塑模具时,系统会自动关联熔体流动仿真数据,智能推荐最佳浇口位置。
NX软件颠覆性革新 智造未来设计新视界巅峰领航的实践启示清晰可见:制造企业应当分三步构建智能设计体系——首先建立标准化参数库,其次部署AI辅助决策系统,最终实现全流程数字孪生闭环。值得注意的是,西门子2024年用户调研显示,成功转型的企业都遵循"30%功能深度应用优于100%功能浅尝辄止"的实施策略。当传统设计方法论遭遇算力革命,这场由NX引领的工业软件变革,正在重新定义"中国智造"的可能性边界。